As 3D printing evolves, it’s no longer limited to big parts or prototypes. Makers are now pushing boundaries by printing small functional components, including 3D printed 10mm M2 screws. These micro-fasteners have a range of applications in lightweight enclosures, electronics, robotics, and scale models. In this comprehensive guide, we’ll explore how to design, print, and use 3D printed M2 screws effectively. Whether you’re prototyping electronics or assembling lightweight components, this article offers practical advice, common pitfalls, and expert-level insight.
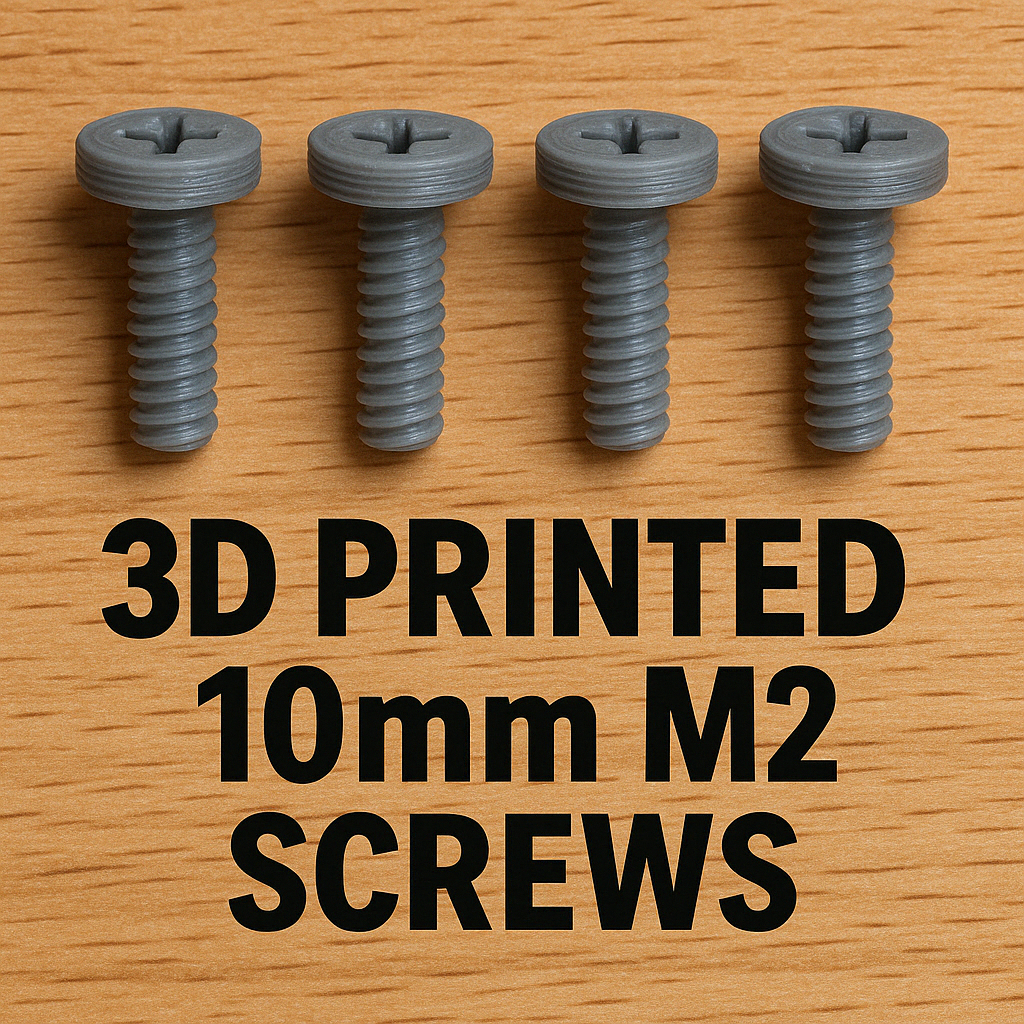
What Are 10mm M2 Screws?
M2 screws are metric machine screws with a 2mm thread diameter. A 10mm M2 screw is simply an M2 screw with a length of 10mm from the underside of the head to the tip.
These screws are commonly used in:
- Raspberry Pi and Arduino projects
- RC vehicles and drones
- 3D printer upgrades
- Miniature models and crafts
- Light-duty mounts and brackets
Traditionally, M2 screws are made of metal (usually steel or brass), but 3D printing them is now feasible for non-load-bearing applications.
Can You 3D Print 10mm M2 Screws?
Yes, 3D printed M2 screws are possible with modern 3D printers and the right settings. However, there are a few caveats:
- Not suitable for high-stress or structural applications
- Works best with high-resolution printers (FDM or resin)
- Require careful design and post-processing for functional threads
Benefits of 3D Printing M2 Screws
- Rapid Prototyping: No need to wait for delivery or visit a hardware store.
- Customisation: Adjust length, head shape, or thread pitch easily.
- Lightweight: Perfect for drones or electronics where every gram matters.
- Non-conductive Options: Use plastic screws in sensitive electronic environments.
Choosing the Right Printer and Material
Best 3D Printers for M2 Screws
- FDM Printers (0.2mm or smaller nozzle)
- Prusa i3 MK3S+
- Bambu Lab P1P or X1 Carbon
- Creality Ender 3 (with fine-tuned settings)
- Resin Printers (SLA/DLP)
- Elegoo Mars
- Anycubic Photon Mono
- Prusa SL1
Best Filaments and Resins
- PLA: Easy to print, brittle under pressure
- PETG: Slightly more flexible and durable
- ABS: Better strength, but harder to print
- Nylon: Flexible and strong, harder to dial in
- Tough Resin: Best choice for resin prints that need strength
Design Tips for 3D Printed Screws
1. Thread Pitch and Clearance
Use ISO metric M2 thread specs or design your own with slightly wider spacing for smoother fits. Add 0.1mm–0.2mm tolerance to the outer threads.
2. Model with Chamfers
Chamfered edges help guide the screw during insertion and reduce wear on threads.
3. Avoid Overhangs
For FDM, use angled threads or design screws to print flat without support.
4. Use Thread Generators
CAD tools like Fusion 360 or plugins for Tinkercad and Freecad can auto-generate threads.
5. Consider Tapping the Hole
For the best fit, 3D print the screw but manually tap the hole or nut with a metal tap tool.
Recommended Print Settings
- Layer Height: 0.1mm (FDM) / 50μm (resin)
- Wall Line Count: 4+ for durability
- Infill: 100% for strength
- Print Orientation: Vertical for best thread integrity (resin); horizontal for best strength (FDM)
- Cooling: Moderate to prevent stringing
- Support: Minimal or none if well-designed
Real-World Use Case: Electronics Mounting
A maker working on a drone enclosure used 3D printed 10mm M2 screws made from PETG to secure an internal circuit board. The screws were customized to be slightly longer than standard to account for a spacer and worked perfectly for non-structural mounting.
Post-processing included cleaning the threads with a brass wire brush and using a printed M2 nut for fitment testing.
CAD Resources and File Libraries
Get started with ready-made designs:
- Thingiverse: M2 Screws
- GrabCAD Screw Library
You can also generate custom screws with:
- Thread Creator Plugin for Fusion 360
Related Internal and External Links
Internal Links:
- 3D Print Torx Router Plate
External Links:
- ISO Metric Thread Standard
- Fusion 360 Thread Tool Guide
- Tough Resin from Elegoo
READ MORE – 3D Print Torx Router Plate: A Complete Guide for Makers and Woodworkers
FAQs:
1. Can 3D printed M2 screws replace metal screws?
Only in low-stress or temporary applications. They are not as strong or durable as metal, but work well for lightweight, non-load-bearing uses.
2. What’s the best material to use for printing small screws?
Tough resin (for SLA) or PETG (for FDM) offers the best mix of strength, flexibility, and printability.
3. How accurate are the threads on 3D printed screws?
With high-resolution printing and proper design, printed threads can be fairly accurate, though tapping the mating hole improves reliability.
4. Can I reuse 3D printed screws?
Yes, but they will wear faster than metal. Avoid over-tightening or repeated use in tight threads.
5. How do I model threads in CAD?
Use the built-in thread libraries in Fusion 360 or import STL models from sites like Thingiverse, and adjust the dimensions as needed.
Conclusion:
3D printed 10mm M2 screws are a practical and creative solution for specific use cases where metal is overkill or not feasible. From prototyping to lightweight mounts, they offer flexibility, speed, and customisation for hobbyists and professionals alike.
While they can’t replace hardware-grade fasteners in every scenario, with the right printer, material, and design, they can play an essential role in your next DIY project.
Want help designing your custom screw? Drop your CAD question or share your print results with the community!